The type
of each joint
When determining the number of links one must
remember that a link may be composed of several different parts. As
long as there is no relative motion between these parts the whole assembly
must be considered as one link.
When determining the number of joints and the type
of each joint the number of contacts between the two bodies is
not important. Remember that there can be only one joint between two
links. What is important is the relative motion that is permitted between
the two links.The shape of the kinematic elements, the material used
is completely unimportant.
When designing the joints, depending on the application
and the available manufacturing facilities, different ways of contact
can be used. If the load to be transmitted is of low magnitude, one
sided contact may be sufficient and the out-of plane moment created
may be negligible. Whereas in case of a mechanism working under heavy
load, a symmetric construction where the contact is on both sides may
be preferred. Furthernore, the pin can be fixed to one link or can be
an integral part of one of the links or can be free.
To increase the load carrying capacity there can be
several contact points between the two links..
Each contact point cannot be treated as a different
kinematic pair. There can be only one kinematic element between two
links.
In the above spatial mechanism there are two contacts
between links links 4 and 5. One contacting pair of kinematic elements
(bottom) will permit 3 rotations and no translation, therefore is a
spherical joint(f=3); the other contacting pair (the top) will permit
three translations and 2 rotations, therefore it is a sphere between
parallel planes joint (f=5). However, there can be one joint between
two links. Therefore one must look at the relative motion that will
be permitted between these two links. First of all, the degree of freedom
of this joint will not be greater than the spherical joint (f=3). The
contact that forms sphere between parallel planes joint will constrain
one of the rotations of the spherical joint. Therefore two rotational
freedoms will be permitted between links 4 and 5 which is known as a
slotted sphere joint..
A mechanism links may be produced in different shapes
depending on the application:
This is a schematic drawing of an
in-line slider-crank mechanism.
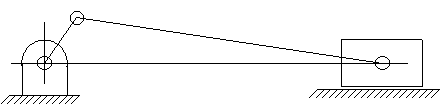
|
The figures shown below can all be
the slider crank mechanism drawings with the same link lengths
but of different link shapes.
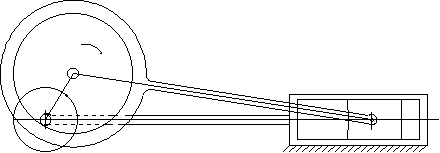
|
|
|
|
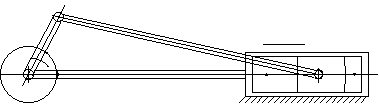
In practice depending on the place the mechanism
is being used, the material the links are made, the shape of
the links, etc. may all change.
|
In cam mechanisms instead of a rigid roller at the
end of the follower, the roller is free to rotate to reduce the sliding
friction. If the degree-of-freedom of this mechanism is evaluated, it
has 4 links 3 revolute and 1 cam pair (j=4, Sfi=5) and the degree-of-freedom
is calculated as (F=3(4-4+1)+5=2) 2. Although the motion of the follower
requires one parameter (rotation of the cam), 2 degrees-of freedom is
correct since the roller is free to rotate about its own axis. In practice,
when we are calculating the degree-of-freedom of the cam pairs, we neglect
the roller and consider this mechanism as composed of 3 links with 2
revolute and 1 cam pair.
In certain other mechanisms, for better force transmission
characteristics, the number of parts that are involved may be increased.
A good example is the planetary gear trains. As far as kinematics is
concerned, one can omit all but one of the planet gears (These mechanisms
can also be considered as mechanisms of critical form, since we require
certain dimensional requirements-such as the dimensions of all the planets
to be the same, i.e. have the same diameter and tooth number-however,
it is not necessary to classify these mechanisms as critical form mechanisms,
since by eliminating all but one of the planets we obtain a mechanism
that obeys the general degree-of-freedom equation).
The degree-of-freedom equation should not, in general,
depend on the link dimensions. There are certain exceptions in which
the degree-of-freedom does depend on the link dimensions. These mechanisms
are said to be in critical
form. We shall call a mechanism to be of permanent
critical form if the general degree-of-freedom equation is
not obeyed through-out the whole phase of the mechanism motion. These
are parallelogram mechanisms (Above figure) or mechanisms
that are derived from Robert-Chebyshev theorem. . In the parallelogram
mechanism shown above, there are 6 links and , 8 revolute joints, thus
the degree-of-freedom obtained from the general degree-of-freedom equation
is: F=3(6-8-1)+8=-1 . However, the mechanism is movable due to the parallelogram
construction.If the opposite link lengths were not equal, the result
obtained from the general degree-of-freedom equation was correct.
In planar mechanisms the permanent critical form is usually the result
of a parallelogram loop. Below, some examples of the use of this parallelogram
mechanism are shown.
Above example is the multiple drill head, to drill
several holes at the same time. This is only possible if the opposite
link dimensions are made equal.(Ifnecessary you can increase or decrease
the number of drills).
Below, the toolbox shown is a very good example of
paralelogram mechanism.
In case of Instantaneous critical form mechanism,the
mechanism is movable only for one instant. At some other position, the
mechanism is a rigid structure and may be unmovable. In general the
degree-of-freedom obtained from the general equation is 0 or negative.
However due to the special dimensions, small amount of motion is permitted
at the design position. Due to the elasticity of the links and joint
clearences the motion is usually of a finite size.
In space mechanisms the permanent critical form is
very frequently encountered. The movability of the mechanism is usually
achieved by the intersection of the axes of two or more joints at one
point. If all the axes of the joints in a space mechanism intersect
at one point, these mechanisms are spherical mechanisms and the degree-of-
freedom of space must be taken as 3 rather than 6. Some of these permanent
critical form mechanisms in space are shown below.
There are lots of different critic form mechanisms
in space. In order to determine the degree-of-freedom of such mechanisms,
a thorough analysis is necessary.
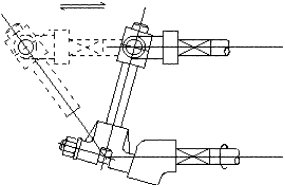
Technical drawing of spatial slide
F=1 |
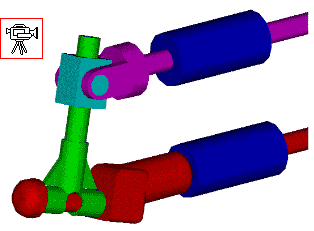
Solid model and its animation |
In the above example, the spatial slide will operate
only if all the revolute joint axis intersect at one point. Two other
similar examples are shown below.
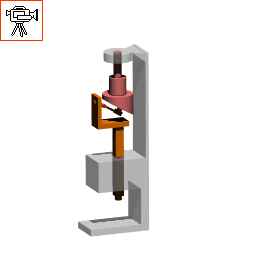
If a planar kinematic chain is formed by sliding and
turning joints only, for a constrained motion and for the mechanism
to obey the general degree-of-freedom equation the following restrictions
must be made:
- If the kinematic elements of a link form sliding
pairs, the axes of the sliding pairs cannot be parallel.
In such a case we have a redundant degree-of-freedom, which is the
translation of that link about the axes of the sliding pairs
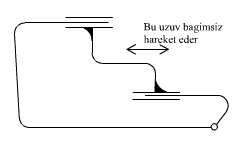
- Binary links of the kinematic chain which have
only prismatic pair elements cannot be directly connected to each
other.
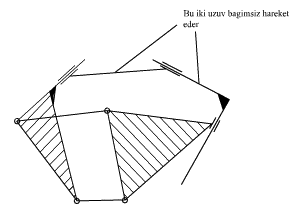
- 3. No closed link loop may have less than two turning
pairs. If there is only one revolute joint, due to the other joints,
which will be prismatic, rotation will not be possible between the
two links connected by the revolute joint.
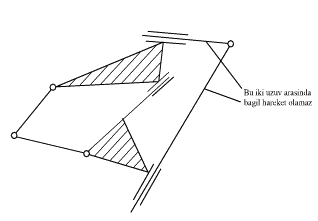
- A three-link loop with revolute and prismatic joints
must be counted as one link. An exception to this case is a three
link-loop with sliding pairs only.
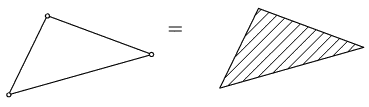
In the above cases there is either redundant freedom
(cases 1 and 2) or immobility (cases 3 and 4)
Another case where the general degree-of-freedom equation
cannot be used, or if used will give an incorrect result is the case
where the degree-of-freedom of space is not constant for the whole mechanism.
For example, consider a spatial four-bar connected in series with a
planar four-bar mechanism. The resulting mechanism has 1 degree-of-freedom.
But in the general degree-of freedom equation the degree of freedom
of space is not clear and neither 3 or 6 degrees-of freedom will not
work.
|
|
Technical Drawing |
Solid Model and Animation |




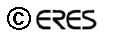