Evolution
of Quality Concepts (cont.)
Armand
V. Feigenbaum 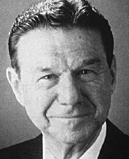
 |
Author
of the book
Total Quality Control |
 |
Total
Quality Control concept and strategies
 |
quality-development |
 |
quality-maintenance |
 |
quality-improvement |
|
|
 |
Full customer
satisfaction, |
 |
System
approach to quality, |
 |
Total
quality control as a cross-functional concept, |
Karou Ishikawa
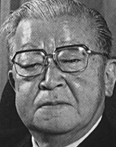
 |
provided leadership in shaping
the Japanese quality movement |
 |
6 quality control
characteristics, What is Total Quality Control?
The Japanese Way
- Company-wide quality control; participation by all members
of the organization in quality control
- Education and training in quality control
- Quality control circle activities
- Quality control audits (for effectiveness)
- Utilization of statistical methods
- Nationwide quality control promotion (including training)
activities
|
|
 |
true quality characteristics: the customer's
view of product performance |
substitute quality characteristics: the
producer's view of product performance |
|
 |
proposed the basis of QFD |
 |
developed seven tools of quality
control, Guide to Quality Control
- Cause-effect (Ishikawa) diagram
- Stratification
- Check sheet
- Histogram
- Scatter diagram
- Pareto chart (vital few, trivial many)
- Graphs and statistical control charts
|
|
 |
Ishikawa's concept of TQC
- Quality first - not short-term profits first
- Consumer orientation - not producer orientation (think from the
standpoint of other party)
- The next process is your customer - breaking down the barrier of
sectionalism
- Using facts and data to make presentations - utilization of
statistical methods
- Respect for humanity as a management philosophy, full participatory
management
- Cross-functional management (by divisions and functions)
|
|
Genichi Taguchi
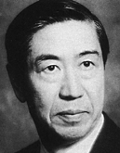
 |
Engineering approach to quality |
 |
importance of variance |
 |
developed robust design, loss
function, SNRs (signal-to-noise ratios) |
 |
identified noise factors
that affect variation |
 |
focused on 3 design levels, Introduction to Quality Engineering: Designing
Quality into Products and Processes
- System design (primary) - functional design focuses on pertinent
technology or architectures
- Parameter design (secondary) - a means of both reducing cost and
improving performance without removing causes of variation
- Tolerance design (tertiary) - a means of reducing variation by
controlling causes, but at an increased cost
|
|
Shigeo Shingo
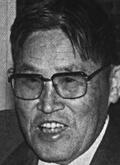
 |
maintains that statistical-based quality
control is not conducive to zero defects |
 |
proposes the poka-yoke (mistake-proofing)
system, Zero Quality Control: Source Inspection and
the Poka-Yoke System
- Use source inspection - the application of control functions at the
stages where defect originate (real-time feedback / feed-forward information)
- Always use 100 percent source inspections (rather than sampling
inspections)
- Minimize the time to carry out corrective action when abnormalities
appear
- Set up poka-yoke (mistake-proofing) devices, such as sensors and
monitors, according to product and process requirements
|
|
  
Copyright © 2008 by the METU. All
rights reserved.
|